Heat Treating Used to Keep Material Hard & Soft
Hardening. Softening. Strengthening.
Heat treating is a group of industrial and metalworking processes used to alter the physical and sometimes chemical properties of a material. The most common application is metallurgical. Heat treatments are also used in the manufacture of many other materials, such as glass. Heat treatment involves the use of heating or chilling, normally to extreme temperatures, to achieve the desired result, such as hardening or softening of a material. Heat treatment techniques include annealing, precipitation strengthening, tempering, normalizing, and quenching.
Tempering Ductility is the ability of a metal to change shape before it breaks. Freshly quenched martensite is hard but not ductile; in fact, it is very brittle. Tempering is needed to add ductility to the material. This usually comes with a small sacrifice in strength. Tempering greatly increases the resistance of some materials to shock loading.
The microstructural changes accompanying tempering include the loss of the acicular martensite pattern and the precipitation of tine carbide particles. The microstructure of quenched and tempered steel is referred to as tempered martensite.
Annealing Two-stage heat-treating produces materials capable of resisting shock and deformation without breaking. The Annealing process is intended to make steel easier to deform or machine.
–Process Annealing – Heating steel or other materials to a temperature just below the A1 for a short time; this makes the metal easier to form.
–Full Annealing – Steel or other materials are heated to 50-100°F above the A3 for hypoeutectoid steels and above the A1 for hypereutectoid steels and is then slowly cooled, making the steel much easier to cut or bend. Cooling must take place very slowly so that course pearlite isn’t formed.
Normalizing – The process of normalizing consists of heating to a temperature above A3 and allowing the part to cool in still air. The actual temperature required for this depends on the composition of the steel, but usually around 1600°F.
If it is heated to a high temperature, the carbon can readily diffuse throughout, and the result is a reasonably uniform composition from one area to the next. The steel is then more homogeneous and will respond to the heat treatment in a more uniform way.
Stress Relieving – When a metal is heated, expansion occurs at a rate proportional to the temperature increase. The reverse action takes place upon cooling. If a metal is heated at on point more than at another, internal stresses are created. Deformation is possible. Heating the metal to 1100°F relieves the stresses created from uneven heating. Also called stress relief annealing.
Precipitation Hardening Also called Age Hardening, these materials are done at a much lower temperature range, normally 900°F to 1150°F, and a specific amount of time. A few examples of these materials are 17-4, 15-5, 13-8, 17-7PH, Custom 450, 455, and 465, just to name a few.
All of these materials are widely used in the Medical, Dental, Marine, Military, and Commercial industries and produce hardness up to 56 HRC depending on the material used.
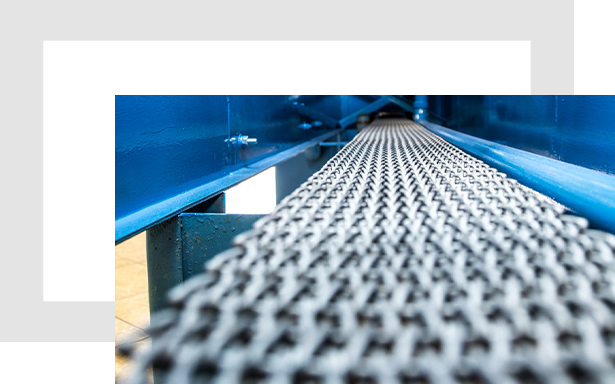